The DMAIC process is at the core of Six Sigma methodology and is used to systematically improve processes by identifying, analyzing, and eliminating problems. DMAIC stands for Define, Measure, Analyze, Improve, and Control, and it provides a structured framework for problem-solving. In this article, we will explore each phase of the DMAIC process and how it helps organizations achieve process improvements.
What is DMAIC?
DMAIC is a problem-solving framework used in Six Sigma projects. It helps organizations improve processes by identifying the root causes of problems and implementing data-driven solutions. Each phase of the DMAIC process builds on the previous one, providing a clear path from problem identification to long-term process control.
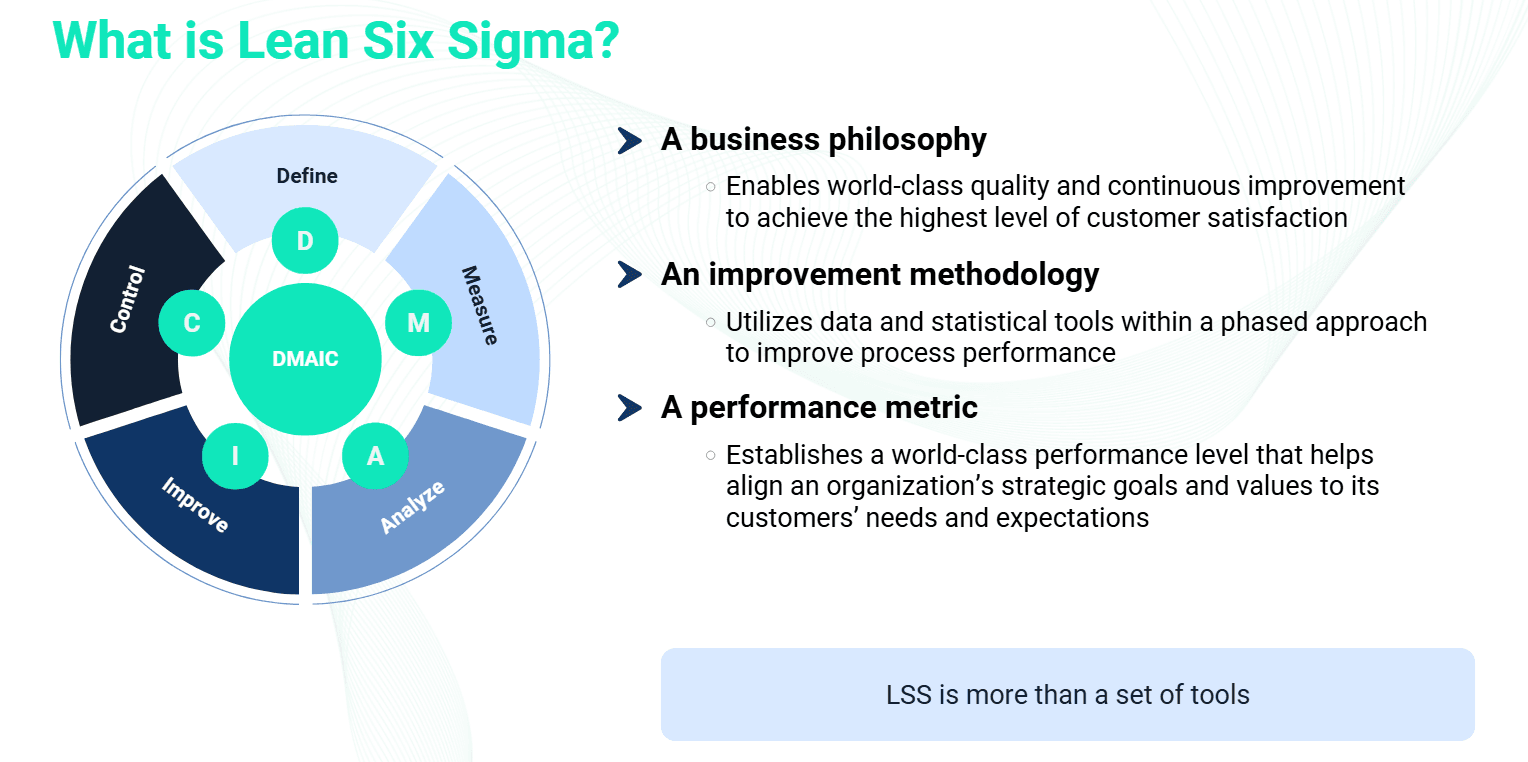
Define Phase
The Define phase is the first step in the DMAIC process and involves clearly defining the problem or opportunity for improvement. This phase sets the foundation for the entire project by establishing the project’s scope, goals, and objectives. During this phase, the project team works closely with stakeholders to understand the problem and its impact on the business.
Key activities in the Define phase include:
- Developing a problem statement that clearly articulates the issue to be addressed.
- Defining the scope of the project, including the boundaries and limitations.
- Identifying key stakeholders and customers affected by the problem.
- Creating a project charter that outlines the goals, deliverables, and timelines for the project.
The Define phase is critical because it ensures that the project team is aligned on the problem and that the project has clear objectives from the outset.
Measure Phase
The Measure phase focuses on collecting data to establish a baseline for the current process. This phase is essential for understanding how the process is currently performing and identifying the extent of the problem. The goal of the Measure phase is to gather accurate data that will be used to quantify the problem and provide a foundation for the Analyze phase.
Key activities in the Measure phase include:
- Identifying key process metrics, such as cycle time, defect rate, or customer satisfaction scores.
- Collecting data on the current process performance.
- Creating a process map or Value Stream Map to visualize the process flow and identify areas of inefficiency.
- Establishing a baseline for process performance, which will be used to measure improvement in later phases.
The Measure phase provides the data needed to fully understand the problem and sets the stage for data-driven analysis in the next phase.
Analyze Phase
In the Analyze phase, the project team uses the data collected in the Measure phase to identify the root causes of the problem. This phase involves statistical analysis and process mapping to understand why the problem is occurring and what factors are contributing to it.
Key activities in the Analyze phase include:
- Conducting root cause analysis using tools like Fishbone Diagrams, Pareto Charts, and 5 Whys.
- Performing data analysis to identify patterns and correlations in the data.
- Validating potential root causes through hypothesis testing or other statistical methods.
The Analyze phase is critical because it moves beyond symptoms to uncover the underlying causes of the problem. By identifying the true root cause, the team can develop effective solutions that address the heart of the issue.
Improve Phase
The Improve phase focuses on developing and implementing solutions to address the root causes identified in the Analyze phase. This is the action-oriented phase where changes are made to the process to eliminate the problem and improve performance.
Key activities in the Improve phase include:
- Brainstorming potential solutions to address the root causes of the problem.
- Testing and piloting potential solutions to ensure they work as intended.
- Implementing solutions that are validated through testing.
- Measuring the impact of the solutions on process performance.
The Improve phase is where real change happens, and the team works to ensure that the solutions lead to measurable improvements in the process.
Control Phase
The Control phase is the final step in the DMAIC process and focuses on sustaining the improvements made in the Improve phase. The goal of this phase is to ensure that the process remains stable and that the improvements are maintained over time.
Key activities in the Control phase include:
- Developing process control plans to monitor the process and ensure it stays within acceptable limits.
- Implementing control charts to track process performance over time.
- Training employees on the new process and ensuring they understand their roles in maintaining it.
- Conducting regular audits to verify that the process continues to perform as expected.
The Control phase is essential for ensuring that the gains made during the project are not lost. It helps organizations maintain long-term process improvements and avoid reverting to old ways of working.
Benefits of Using DMAIC
The DMAIC process provides several key benefits for organizations seeking to improve their processes:
- Structured Approach: DMAIC offers a clear and structured framework for problem-solving, ensuring that projects stay on track and focused on measurable outcomes.
- Data-Driven Decisions: By relying on data analysis, DMAIC ensures that decisions are based on evidence rather than assumptions, leading to more effective solutions.
- Sustainable Improvements: The Control phase ensures that improvements are sustained over time, preventing backsliding and ensuring long-term success.
- Cross-Functional Collaboration: DMAIC encourages collaboration across departments, bringing together different perspectives and expertise to solve complex problems.
Conclusion
The DMAIC process is a powerful tool for improving business processes and achieving lasting improvements. By following the Define, Measure, Analyze, Improve, and Control phases, organizations can systematically identify and eliminate problems, resulting in more efficient and effective operations. DMAIC is not only a key component of Six Sigma but also a valuable problem-solving framework that can be applied to any industry or business process. Organizations that embrace DMAIC as part of their continuous improvement efforts are better equipped to meet customer needs, reduce costs, and enhance overall performance.